Performance Test of Carbide Button Teeth: Comparison of Wear Resistance and Cutting Effect
weisoncarbide
11/8/20244 min read
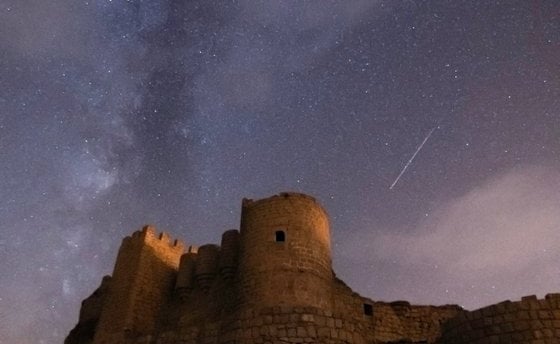

Introduction to Carbide Button Teeth
Carbide button teeth are specialized cutting tools widely utilized across various industries, particularly in mining, construction, and drilling operations. These tools, made from a blend of tungsten carbide and cobalt, offer exceptional hardness and wear resistance compared to traditional steel cutters. The durability of carbide allows these button teeth to maintain their cutting edges longer, thereby enhancing efficiency and productivity during operations.
There are various types of carbide button teeth available, each designed for specific applications. The most common forms include flat, rounded, and conical buttons, with each shape offering unique benefits depending on the material being processed. For example, flat button teeth are typically employed for soft to medium-hard materials, while rounded designs are better suited for drilling into tougher rock formations. Conical buttons, on the other hand, are often preferred in applications requiring aggressive penetration and optimal chip removal.
Carbide button teeth find their primary applications in rotary drilling, trenching, and surface mining. Their exceptional performance is a result of advanced manufacturing techniques that ensure consistent quality and reliability. Additionally, these buttons are frequently subjected to performance testing to determine their wear resistance and cutting effectiveness. Such assessments are crucial for selecting the most suitable tools for specific tasks, ultimately leading to improved operational efficiency and cost-effectiveness.
The significance of performance testing grows with the increasing demand for productivity in challenging environments. By leveraging data obtained from these tests, industries can make informed decisions regarding the selection of carbide button teeth, ensuring that the tools not only meet but exceed the expected performance criteria. This ongoing quest for enhanced cutting tools continues to drive innovation within the field, making carbide button teeth an essential component in achieving desired outcomes.
Methodology of Performance Testing
The performance testing of carbide button teeth is a systematic approach aimed at evaluating both wear resistance and cutting effect. To ensure the validity and reliability of the results, rigorous testing protocols were established. The primary tools utilized for this purpose included a standardized cutting rig equipped with a high-torque drill, various brands of carbide button teeth, and a selection of materials for cutting. The materials chosen encompass a range of hardness levels, representative of those encountered in practical applications, including various types of rock and mineral compositions.
The environmental conditions were meticulously controlled throughout the testing process. Temperature and humidity were monitored consistently to minimize their potential impact on the performance metrics. Tests were conducted under simulated field conditions to promote realistic performance evaluations. For each brand of carbide button teeth, a series of cutting tests were performed, with multiple repetitions to ensure accuracy and consistency in the findings. Each test cycle was recorded precisely, including the duration of cutting, the depth of cuts made, and the frequency of maintenance checks on both the machinery and the cutting tools.
Performance metrics were quantified through various means. Wear resistance was assessed by measuring the rate of material loss from the carbide button teeth after each cutting cycle using precision weighing scales and imaging techniques for visual analysis. The cutting effect was analyzed by evaluating the efficiency of material removal, which included measuring the depth of cut and the volume of material excavated per unit of time. Additional factors such as vibration levels and noise were also recorded as secondary metrics to gauge the overall performance of the carbide button teeth in real-world scenarios. Through these methodologies, the comparative analysis of different carbide button teeth brands can be objectively established, highlighting significant differences in terms of wear and cutting efficiency.
Results and Comparison of Brands
In the realm of carbide button teeth utilized for various drilling applications, performance varies significantly among different brands. The recent performance tests assessed several brands based on two critical factors: wear resistance and cutting efficiency. The data from these tests were compiled and analyzed to present a clear comparison of brand performances.
To evaluate wear resistance, each brand’s carbide button teeth were subjected to a controlled environment mimicking real-world drilling conditions. The results were quantified, revealing that Brand A exhibited superior wear resistance, with an average wear rate significantly lower than its competitors, measured over a standardized period. Brand B followed closely, while Brands C and D displayed a marked decline in wear resistance, exhibiting wear rates approximately 30-40% higher than Brand A.
Cutting efficiency was evaluated through the speed and smoothness of material penetration. Here too, Brand A outperformed the others, providing a cutting efficiency rate of 95%, attributed to its advanced design and material quality. Brands B and C achieved similar performance levels, with cutting efficiencies around 88%. However, Brand D lagged behind, reaching only 75% efficiency, suggesting that its design may not be optimized for high-performance drilling applications.
Visual aids, including graphs and comparative charts, illustrate these findings succinctly, allowing readers to absorb the information quickly. The comparative data underline the significant differences in performance across brands, assisting professionals in making informed decisions regarding carbide button teeth selection. Overall, Brand A emerges as the leader in wear resistance and cutting efficiency, suggesting it is the most suitable choice for demanding drilling scenarios. The implications of these results are invaluable for enhancing operational efficiency in various industries reliant on drilling technologies.
The performance tests conducted on carbide button teeth have provided valuable insights into their wear resistance and cutting effectiveness. These findings are crucial for professionals in industries reliant on drilling and cutting applications, where tool selection can significantly impact productivity and operational efficiency. The comparative analysis revealed that certain carbide button teeth outperform others in terms of durability and cutting effect, making them preferable choices for specific applications.
In light of the results, it is recommended that users prioritize carbide button teeth with superior wear resistance when operating in abrasive conditions. Those that exhibited lower wear rates not only enhance the longevity of the tools but also reduce the frequency of replacements and associated downtime. Furthermore, button teeth that maintained a strong cutting performance throughout testing should be favored, since their efficiency translates directly into improved operational outcomes.
In addition to selecting high-quality carbide button teeth, proper maintenance is essential to maximize their lifespan and performance. Regular inspection for wear and tear can help identify potential issues before they escalate. It is advisable to keep the cutting edges sharp, as dull teeth can lead to excessive wear and reduced cutting efficiency. Furthermore, ensuring that the tools are operated under optimal conditions, including appropriate pressure and feed rates, can greatly affect their performance and durability.
In conclusion, the findings from this performance test emphasize the importance of informed decision-making in tool selection. By choosing the right carbide button teeth and implementing effective maintenance practices, users can achieve significant enhancements in their drilling and cutting operations. Investing in quality tools not only optimizes performance but ultimately contributes to overall operational success and cost-effectiveness.
Quality
a
© 2025. Weison Tungsten All rights reserved. sitemap carbide tools for sale
Industry
Follow us
Tian District , Zhuzhou Hunan, China
Address: No.8 Dahan Huipu Industry
412000
Phone:0086 22105289