How to Maximizing Efficiency
weisoncarbide
2/21/20254 min read
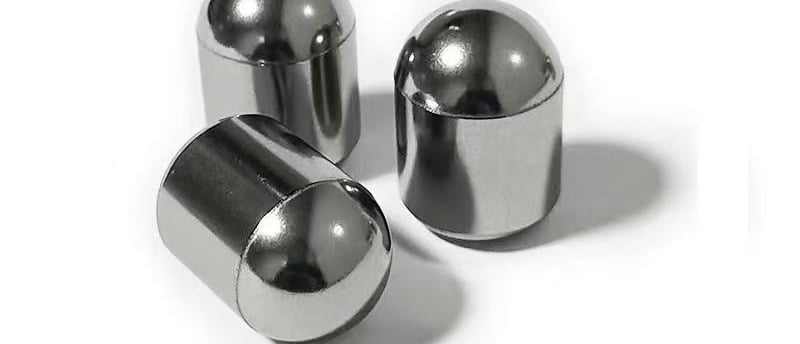
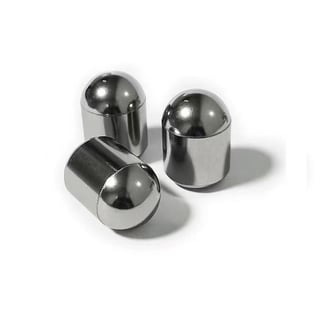
Carbide ball teeth are essential components used in various industries, prominently in earth-moving and drilling operations. Composed primarily of tungsten carbide, these tools are engineered to withstand high levels of wear and stress. The composition of carbide ball teeth grants them remarkable hardness and durability, making them ideal for applications that require robust performance in challenging environments.
In the field of construction, for instance, carbide ball teeth are crucial for excavators, bulldozers, and other machinery involved in earthworks. Their design allows for efficient excavation and material handling, ensuring that operations are carried out smoothly and effectively. Similarly, in the mining sector, these teeth are used in drills and cutters, significantly enhancing the productivity of mineral extraction processes. Their ability to penetrate hard rock formations with minimal wear is a vital aspect of their function, as it directly contributes to reduced downtime and maintenance costs.
Moreover, carbide ball teeth are not limited to heavy machinery; they also find applications in several manufacturing processes where precision cutting or machining is required. This versatility underscores their importance across different industries, as they are tailored to meet specific operational demands. For instance, in the oil and gas sector, these teeth are employed in rotary drilling operations, where their durability plays a key role in executing successful drilling programs.
Proper maintenance of carbide ball teeth is paramount to ensure optimal performance and extend their service life. Regular inspection and timely replacement, when necessary, help maintain machinery efficiency and safety. Ultimately, understanding the functionality and applications of carbide ball teeth facilitates better decision-making regarding their usage and care, enabling industries to maximize their operational effectiveness.
Best Practices for Carbide Maintenance
Maintaining carbide ball teeth is crucial to ensure their effective performance and longevity. To begin with, proper cleaning procedures should be established. After each use, carbide teeth must be thoroughly cleaned to remove dirt, debris, and any residual materials that may cause wear. A gentle detergent solution can be utilized along with soft brushes to avoid scratching the surface, which could compromise their structural integrity. Ensuring that all areas are cleaned will also facilitate a better inspection process.
Regular inspection routines complement the cleaning process and play a significant role in identifying potential issues early. Technicians should check for signs of wear, such as chipping or cracking, and assess the overall condition of the teeth. An effective strategy includes visual inspections combined with measurements of critical dimensions to detect any deviations from manufacturer specifications. Implementing a standardized checklist can aid in consistency during inspections, ensuring that all crucial aspects are considered.
Storage conditions can significantly impact the efficacy of carbide ball teeth. It is important to store them in a dry, cool environment to prevent moisture from affecting their durability. Ideally, carbide teeth should be kept in protective cases or containers that minimize exposure to dust and moisture. Ensuring that they are slightly elevated and not in direct contact with the ground can also prevent potential contamination from soil and other elements.
In addition to cleaning, inspection, and storage, end-users should be educated on the signs of wear and the importance of preventative maintenance. This can include understanding when to replace the carbide teeth based on performance indicators and usage frequency. By following these best practices, wholesalers can empower end-users to maintain their carbide ball teeth efficiently and prolong their service life, ultimately maximizing productivity.
Identifying Signs of Wear: When to Replace Carbide Ball Teeth
Carbide ball teeth are essential components used in various industrial applications, particularly in the fields of mining, construction, and road maintenance. Over time, these tools undergo wear and tear due to their constant exposure to abrasive materials and demanding working conditions. Identifying the signs of wear is crucial for ensuring optimal performance and minimizing costly downtimes. Manufacturers and equipment users should stay vigilant to recognize when it is time to replace carbide ball teeth.
Common indicators of wear include visible damage such as cracking, chipping, or significant surface erosion. These patterns often correlate with a decline in performance, leading to inefficiencies in material handling or rock cutting processes. Furthermore, if operators notice excessive vibration or a decrease in cutting precision, it may indicate that the carbide ball teeth have surpassed their usable life. Regular inspection of the teeth's condition can reveal these symptoms early, enabling timely replacement and preventing further damage to associated machinery.
Another critical sign of wear arises from performance metrics. If the productivity of the tool drops, or if the operating temperature significantly increases during use, these could signal that the carbide ball teeth are poorly functioning. It's prudent to implement a routine maintenance schedule that incorporates regular checks on the tool's performance and the visual assessment of the teeth. By prioritizing these inspections, users can better estimate the remaining service life of carbide ball teeth and take appropriate action when needed.
In conclusion, recognizing the signs of wear on carbide ball teeth is vital for maintaining efficiency and prolonging service life. By monitoring for visible damage, performance fluctuations, and conducting routine inspections, users can make informed decisions about replacement, ultimately reducing operational interruptions and enhancing productivity.
Implementing a Maintenance Schedule: A Strategic Approach
Establishing a comprehensive maintenance schedule for carbide ball teeth is imperative for extending their service life and enhancing operational efficiency. A well-structured maintenance plan should incorporate regular inspections and defined maintenance tasks tailored to the particular usage conditions of the equipment.
To begin, it is essential to determine the appropriate frequency of inspections. Typically, a bi-weekly or monthly schedule is advisable, depending on the level of activity and wear observed. For equipment subjected to heavy usage or operating in harsh environments, more frequent inspections may be warranted. Conducting these inspections can help identify wear patterns and detect early signs of failure, which can then inform timely maintenance actions.
Prioritization of maintenance tasks is another key element in a strategic maintenance approach. Prioritizing tasks based on usage rates involves assessing which carbide ball teeth experience the most wear and, therefore, require more attention. Additionally, environmental conditions such as humidity, temperature, and presence of abrasive materials should influence maintenance priorities. For example, if the teeth are frequently used in highly abrasive materials, they may need more frequent sharpening or replacement.
Maintaining a detailed log of all maintenance activities provides further benefits. Logbooks can record inspection results, maintenance actions taken, and any noted performance changes. This documentation not only supports ongoing efficiency but also allows for the identification of trends in wear and is a valuable resource for future decision-making regarding replacements and upgrades. This systematic approach benefits both wholesalers, as it can inform inventory management, and end users, as it enhances productivity by ensuring reliable operation of their drilling equipment.
By implementing a strategic maintenance schedule for carbide ball teeth, users can achieve significant long-term benefits, maximizing their operational lifespan and ultimately yielding higher productivity and performance levels.
Quality
a
© 2025. Weison Tungsten All rights reserved. sitemap carbide tools for sale
Industry
Follow us
Tian District , Zhuzhou Hunan, China
Address: No.8 Dahan Huipu Industry
412000
Phone:0086 22105289