How to achieve breakthroughs in high-wear environments
weisoncarbide
9/20/20244 min read
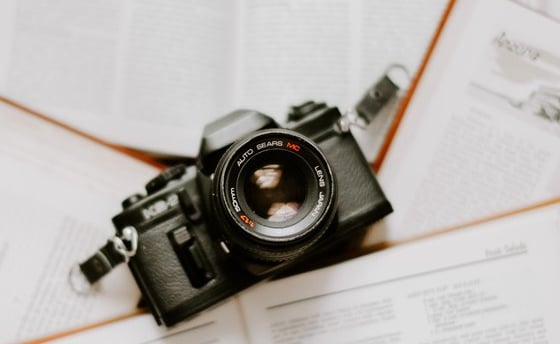
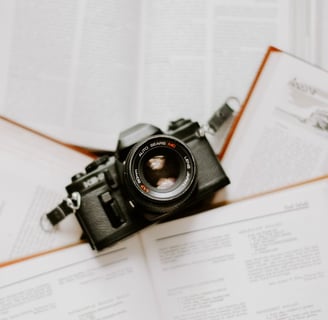
Introduction to Tungsten Carbide in Wear Applications
Tungsten carbide is a composite material consisting primarily of tungsten and carbon, which is renowned for its exceptional hardness and wear resistance. This remarkable composite is created by a process that involves sintering metallic tungsten powder with carbon at extremely high temperatures, resulting in a dense and robust material. The typical hardness of tungsten carbide ranges between 1400 and 2400 HV (Vickers hardness), positioning it as one of the hardest materials available, making it suitable for high-wear applications across various industries.
In many industrial sectors, equipment and machinery are subjected to significant wear and tear, leading to costly downtimes and maintenance. The challenges associated with wear can severely impact operational efficiency and product quality. Traditional materials often succumb to abrasion, erosion, and other forms of wear, necessitating frequent replacements. In this context, wear-resistant carbide parts emerge as a viable solution, mitigating the adverse effects of wear on components, stretching their service life, and ultimately enhancing productivity.
Tungsten carbide is particularly effective in high-wear environments, such as those found in mining, construction, and manufacturing. For example, in the mining sector, the integration of tungsten carbide components in drilling tools has led to improved performance due to their robust hardness and strength. Similarly, in construction, the use of wear-resistant carbide parts in machinery operates under extreme pressures and abrasive conditions, ensuring durability and reliability. Additionally, in manufacturing, tungsten carbide tools offer significant advantages in machining applications, resulting in higher accuracy and reduced tool wear rates.
This comprehensive overview highlights the exceptional properties of tungsten carbide and its essential role in contemporary industries facing wear challenges. The adoption of wear-resistant carbide parts is increasingly becoming key to maintaining operational efficiency and minimizing costs in high-wear applications.
Benefits of Tungsten Carbide Parts in Increasing Productivity
Tungsten carbide parts play an integral role in enhancing productivity across various industries, particularly in sectors characterized by high-wear applications. The introduction of wear-resistant carbide components can significantly reduce downtime caused by equipment failure and maintenance, allowing for smoother and more efficient operations. For instance, many manufacturing plants have reported considerable increases in production rates after integrating tungsten carbide parts into their machinery.
One of the primary advantages of tungsten carbide components is their exceptional hardness and durability compared to traditional materials. This superior strength results in fewer breakdowns and interruptions, which are often costly in terms of both time and resources. A notable example can be observed in the mining industry, where tungsten carbide drill bits have been employed to extend operational life drastically. As a result, companies witness substantial reductions in the frequency of part replacement, translating to more uninterrupted production cycles and increased output.
Furthermore, the operational efficiency associated with tungsten carbide parts extends beyond mere longevity. These components often contribute to improved performance characteristics, enhancing the overall effectiveness of machinery. For instance, equipment fitted with wear-resistant carbide components may operate more smoothly and at higher speeds, leading to a more cohesive workflow within the production line. Moreover, the precision that tungsten carbide parts offer can minimize material waste, thus streamlining processes and contributing further to a facility's productivity.
In many scenarios, the integration of tungsten carbide parts has not only improved performance metrics but also provided significant cost savings. Companies that invest in these durable components tend to experience lower maintenance costs and fewer operational disruptions, allowing for better resource allocation and management. Overall, the inclusion of tungsten carbide parts in high-wear applications represents a strategic approach to increasing productivity across various industrial sectors.
Cost-Effectiveness: Reducing Maintenance Expenses
The implementation of wear-resistant carbide parts, particularly tungsten carbide, has proven to be a strategic initiative for industries operating under high-wear conditions. One of the primary financial benefits of these materials lies in their exceptional durability, which translates into a significant reduction in maintenance expenses. With heightened resistance to wear and tear, tungsten carbide parts require less frequent maintenance interventions, which directly correlates with lowered operational costs over time.
Industries such as mining, manufacturing, and construction often face challenges stemming from equipment breakdowns and component failures. By integrating tungsten carbide components, these sectors can expect extended operational lifespans that mitigate the need for repeated repairs. For instance, studies have shown that businesses using wear-resistant carbide parts reduce the frequency of equipment downtime by approximately 30-50%. This noticeable decrease allows for smoother operations and increased productivity, ultimately boosting profit margins.
Another financial implication involves increasing the intervals between part replacements. Traditional materials may necessitate replacement every few months, whereas tungsten carbide parts can often endure for years under similar operating conditions. This longevity not only decreases the number of emergency purchases but also allows companies to allocate their budgets toward other critical areas rather than continual replacements. According to market analyses, organizations report as much as a 25% improvement in their return on investment by transitioning to these durable alternatives.
In summary, the integration of wear-resistant carbide parts, specifically tungsten carbide components, is a cost-effective strategy that minimizes maintenance expenses. By reducing maintenance frequency, extending part replacement intervals, and delivering an overall better return on investment, businesses can achieve substantial long-term savings while maintaining operational efficiency. The transition to these advanced materials, therefore, represents not merely a technical upgrade, but a fundamental shift towards more sustainable financial practices in high-wear applications.
Extending Service Life of Equipment with Tungsten Carbide
Tungsten carbide is renowned for its exceptional hardness and wear resistance, making it a prime choice in applications where equipment faces rigorous conditions. The unique properties of tungsten carbide parts significantly contribute to extending the service life of machinery and equipment, providing advantages that are both economic and operational. The material's high density and toughness allow it to withstand extreme wear and degradation, common in various industrial environments, such as mining, construction, and manufacturing.
The mechanisms through which tungsten carbide resists wear are multi-faceted. The carbide's molecular structure, a composite of tungsten and carbon, forms a very strong bond that enhances its hardness levels, allowing it to endure harsh abrasives without degrading quickly. This resilience not only means longer replacement intervals for components, thereby reducing operational downtime, but it also allows for more reliable performance under demanding conditions, ensuring that machinery operates efficiently over time.
Furthermore, the implications of using tungsten carbide parts extend beyond mere longevity. By investing in these robust components, organizations can significantly reduce capital expenditure on new equipment. The extended service life translates to lower maintenance costs and fewer disruptions in production, contributing to overall operational stability. Additionally, testimonials from industry experts highlight the effectiveness of tungsten carbide in minimizing wear-related disruptions, further reinforcing the notion that these components are a prudent investment for any high-wear application.
In light of these advantages, it is evident that integrating tungsten carbide parts into machinery not only promotes durability but also enhances prolonged operational efficiency. The decision to utilize wear-resistant carbide parts can ultimately lead to significant long-term savings and improved productivity in various industrial sectors.
Quality
a
© 2025. Weison Tungsten All rights reserved. sitemap carbide tools for sale
Industry
Follow us
Tian District , Zhuzhou Hunan, China
Address: No.8 Dahan Huipu Industry
412000
Phone:0086 22105289